Fairfield Tubular Steel Operations Team Travels to Germany for Steelmaker to Steelmaker Training
On March 7, team members from Fairfield Tubular Steel Operations (FTSO) traveled to Germany to attend Steelmaker to Steelmaker training in Kehl, Germany with Badische-Stahl Engineering GmbH (BSE). Although the training was cut short due to travel restrictions related to COVID-19, the team returned to Alabama with a new understanding of electric arc furnace (EAF) operations.
The training included multiple classroom sessions along with hands-on training in their manufacturing facility. The BSE facility is operating two electric arc furnaces, two ladle furnaces, and two continuous casters.
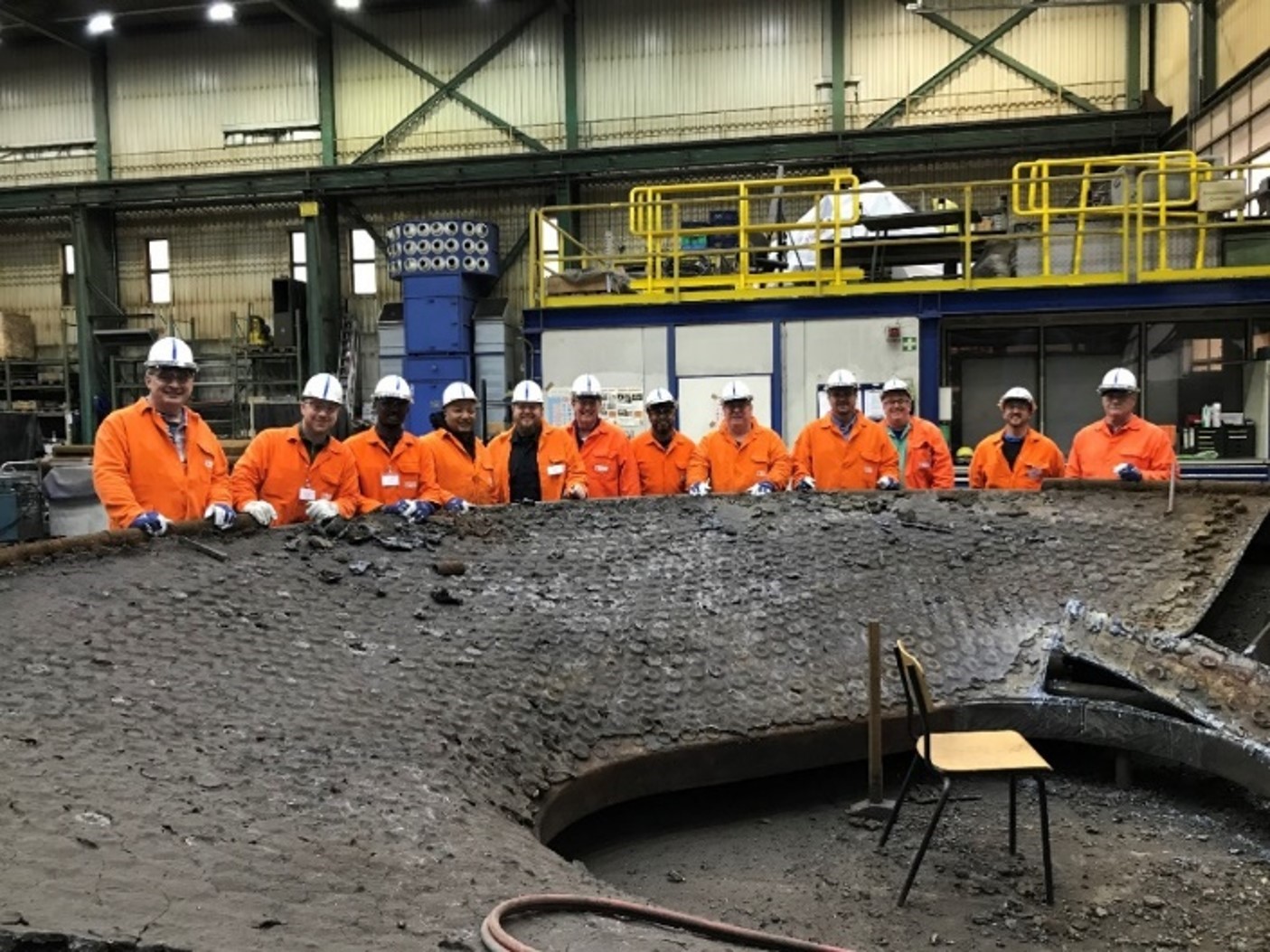
The training kicked off with a company introduction and an overview of the personal protective equipment required for working in the steelmaking areas of the facility. From there, the team toured the scrap yard, which is the start of the EAF process. BSE uses gantry cranes for their scrap yard operation and they have dedicated scrap buckets for each furnace. The cars are controlled remotely by the scrap yard operator pulpit then handed off to the crane operator to maintain continuous visibility.
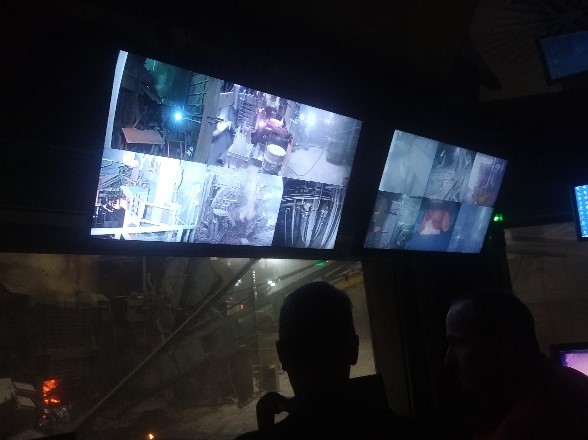
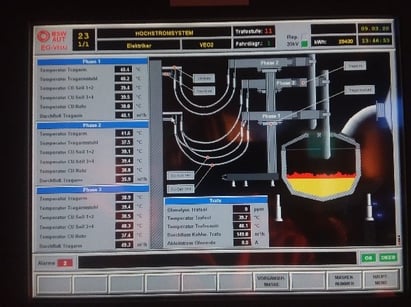
Next, the team toured the plant to visit the electric arc furnace, continuous caster and rolling mill operations. The tour guide explained each process and they watched the operators at work.
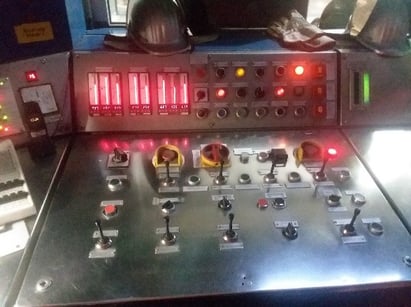
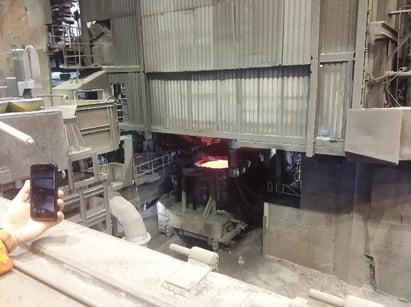
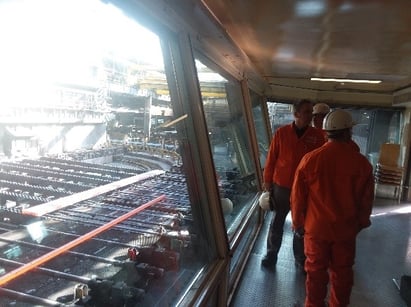
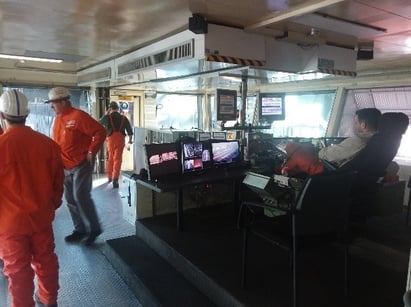
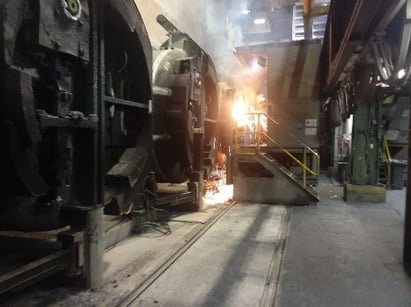
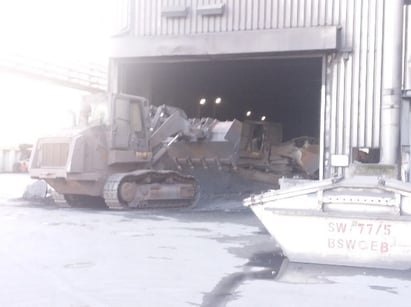
Next, the team visited their central maintenance workshop. BSE’s maintenance group is responsible for maintenance for their entire facility. While visiting the workshop, the training included witnessing the repair of a damaged cooling panel. BSE technicians demonstrated the failure point on the panel and the repair process to return to operating condition. The team also visited the tractor shop and the furnace roof repair area of the facility.
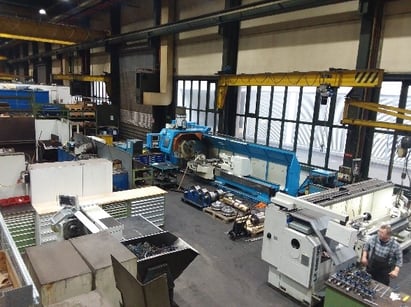
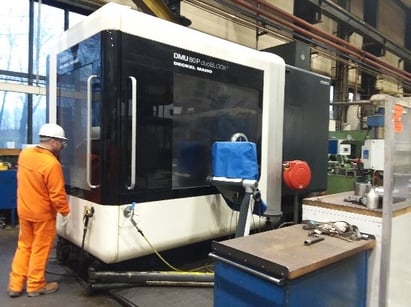
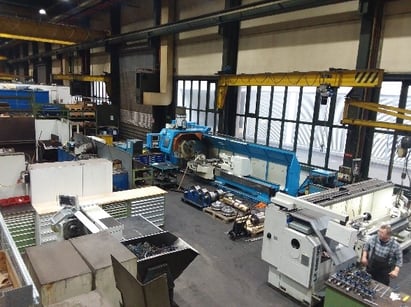
Although COVID-19 travel restrictions required the Fairfield team to return home early, they returned with new knowledge of the EAF process to apply to Fairfield EAF operations.